Guided implant surgery
15 January 2025CBCT 3D training: From cone beam to surgical guide
15 January 2025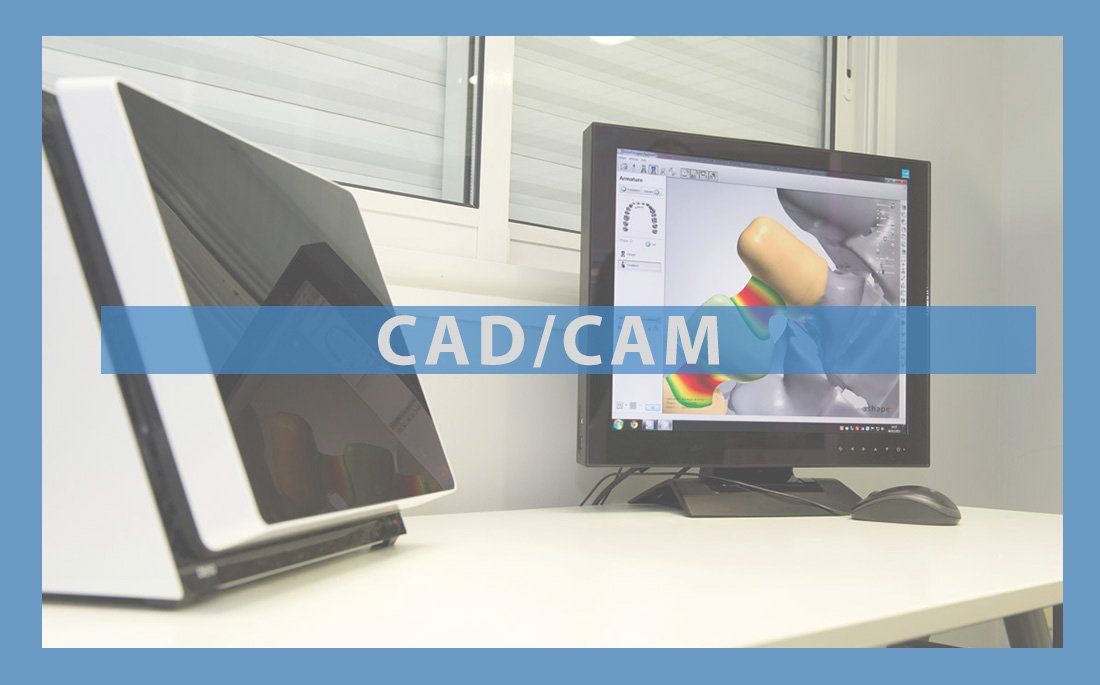
CAD/CAM: an essential partner in modern dentistry
Introduction:A brief history
Initially developed in the aeronautical and automobile industry in the 1960s, in order to standardise the production of routine, repetitive forms, CAD/CAM’s dentistry application was considered an ambitious and somewhat fanciful project, each prosthetic piece being unique and specific to the individual patient.
In 1973, François Duret had the idea of transferring this concept to making dental prosthetics, and thus became the inventor of dental CAD/CAM, the foundations of which he discussed in his paper “Optical impression”.
Thanks to the work of F. Duret, CAD/CAM was born and went on to revolutionise the world of dentistry.
This technology has continued to evolve and improve ever since in the field of odontology, carving itself a reputation as an indispensable tool in the digital age.
The first part of this article examining dental CAD/CAM will be dedicated to a definition of the CAD/CAM chain and its various components and their characteristics. We will then look at the various classifications within the dental CAD/CAM chain, and discuss its applications, benefits and limitations.
Definition
The dental CAD/CAM chain (Computer Aided Design / Computer Aided Manufacturing) is a collection of coordinated technological resources for recording (acquisition) analogue clinical data in digital format and virtual modelling, before producing a tangible bespoke medical device.
It therefore concerns all odontology specialties requiring bespoke medical devices.
Digital flows and components in the CAD/CAM dental chain
A full CAD/CAM dental chain comprises 4 links separated by interfaces:

1st Iink: Data acquisition
Acquisition involves digitising clinical data, followed by a processing stage. This can be done directly in the mouth using an intra-oral camera, or by scanning plaster moulds or impressions.
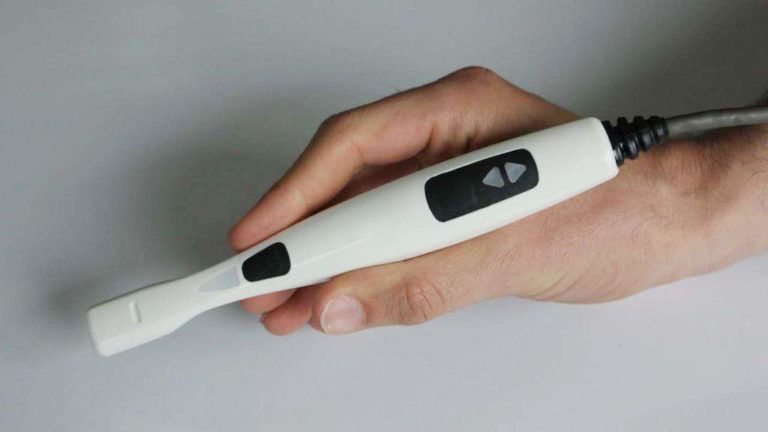
Figure 1 intra-oral camera
2nd link:CAD
CAD (computer aided design) is the process of creating virtual objects using a graphic representation. It includes a stage prior to the prosthetics design stage involving the “post-processing” of points obtained during the acquisition stage using optical impressions. At the end of this stage, the virtual model appears on the screen after digitisation.
3rd link:CAM
CAM (computer aided manufacturing) is the process of making objects; transforming a virtual object (created by CAD) into a material object. This involves dedicated software to generate toolpaths, determining the tools’ positions during manufacturing.
4th link:NCMT (Numerical control machine tools)
This is the fourth and last component in the CAD/CAM dental chain, and is responsible for manufacturing.It’s a programmable machine tool fitted with a numerical control.
The manufacturing process is conducted either:
–By subtraction (by removing materials): we talk about subtractive manufacturing, primarily machining via milling.
–By addition (by adding materials): we talk about additive manufacturing, better known as 3D printing. The main additive processes for formatting are stereolithography (SLA), fused deposition modelling (FDM), laser micro-fusion (LM) and selective laser sintering (SLS).
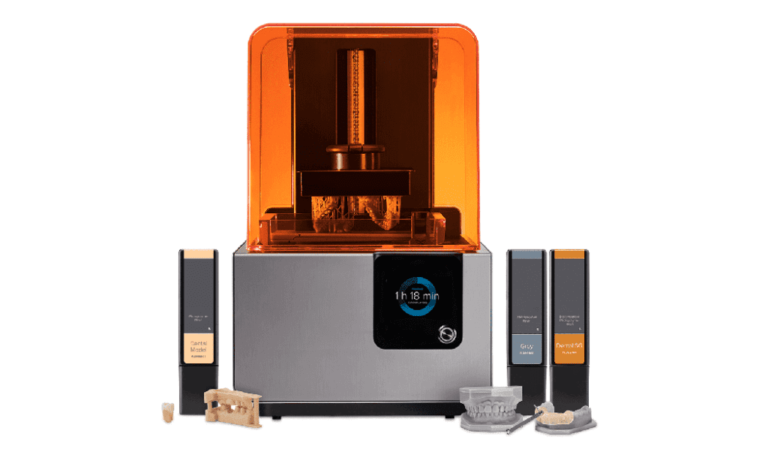
Figure 2 (SLA technique) 3D printer
SLA | FDM | LM | SLS |
Stereolithography via photopolymerisation (stereolithography apparatus) | Fused deposition modelling | Laser micro-fusion (selective laser melting) | Selective laser sintering |
Chemical process Gradual polymerisation using laser beams from a sensitive special resin. Once the layer has solidified, the laser continues to sweep the liquid resin basin, heating it to polymerise it and make it harden, until the entire object has been formed in successive layers. | Physical process Thermoplastic polymer filament clump, heated to its plasticity temperature, layer by layer using a nozzle to form the desired object. | Physical process Clump of successive layers linked to a laser sweeping a metal powder bed to melt it until the metal piece forms | Physical process Clump of successive layers linked to a laser sweeping each layer to enable selective laser sintering until the desired model is obtained |
Direct, semi-direct or indirect CAD/CAM?
Developments in CAD/CAM mean that we are now in a position to distinguish three different methods:
Direct CAD/CAM
Enables the practitioner to construct a prosthesis in one single session. All stages are carried out in their surgery. The intra-oral optical impression is processed on site until it has been restored; inlays, onlays, ceramic veneers, single crowns or temporary bridges.
Semi-direct CAD/CAM
Requires at least one visit to a dental surgery; the data acquired by the practitioner can be processed in the surgery to carry out the CAD, or transmitted to an online laboratory or machining centre in real time, for immediate interaction with the manufacturer, to produce the infrastructure as well as the cosmetic element.
Indirect CAD/CAM
The practitioner produces a standard manual chemical impression that they then send to the prosthetist or machining centre. All stages in the chain are therefore outsourced.
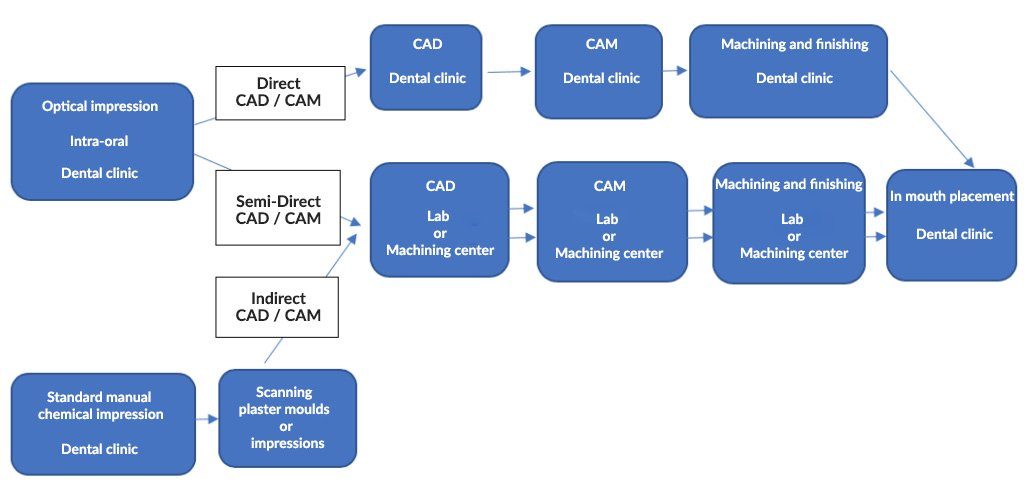
Semi-direct and indirect techniques require laboratories or machining centres to construct more complex restorations using materials that are more difficult to work with in a dental surgery.
Open chain versus closed chain
This concept defines the ability to intervene in a particular link of the CAD/CAM chain, or to change the link in a digital flow.
Closed system or “closed” CAD/CAM chain
In the first instance, all chain components are stipulated by the manufacturer. Once the acquisition stage is complete, nothing can exit the chain and no data export is possible, except for the end product.
Open system or “open” CAD/CAM chain
The practitioner has the option to acquire the various links from different manufacturers, in line with their needs and specific characteristics of each component. It is possible to exit the chain after each stage and also to export files. This type of system makes it possible to modify a whole link or certain parameters, and to access the data obtained.
Compatibility concept
It’s the “compatibility” between the various selected links in the chain that dictates the ability of two digital systems (software or hardware) to exchange data without altering the information. This represents the minimum requirement to integrate two consecutive digital systems in the same digital flow. This constitutes a major criterion when choosing a CAD/CAM chain.
What materials are used in CAD/CAM techniques?
Compared with traditional techniques, CAD/CAM offers a more varied palate of materials in order to fulfil all restoration types. The materials used depend on the process adopted: manufacturing by subtraction or addition; they are chiefly aesthetic ones: resins, all kinds of ceramics (feldspathics, vitro-ceramics, aluminous, alumina and zirconia crystals) and hybrid materials.
Practitioners now have blocks of full-tone materials as well as shaded multi-chromatic blocks in one direction (Empress CAD Multi, etc.) or several directions (MkII Real Life), and even with variable translucency levels (Empress CAD and eMax CAD). Manufacturers also have dyed crystal ceramic blocks.
This is how CAD/CAM has been able to promote materials other than metal alloys and products used in traditional techniques, leading to the standardisation of all-ceramic restorations.
What applications does CAD/CAM have?
The use of CAD/CAM technology has led to the improvement of existing therapeutic solutions and paved the way for new solutions.
The application fields for CAD/CAM range from restorative dentistry and prosthetics to implantology, oral surgery and orthodontics.
This technique can be used for indirect restorations (inlays and onlays), single and multiple fixed prostheses, inlay cores, dental veneers, supra-implantary prostheses (bonded or screw-in), and even temporary prostheses.
It can also be used for removable prostheses and removable prostheses on implants.
For adjoint prostheses, dedicated software is capable of designing complete prosthetic bases and metal partial prosthesis frames, and to simulate the patient’s occlusion on a virtual articulator.
It is also used to make maxillo-facial prostheses. The manufacturing processes and materials are different for each application, but the digital flow remains largely the same.
In implantology, CAD/CAM can be used to make individualised pillars, customised implant bars and implant surgical guides to guide the surgical procedure for implant placement.
CAD/CAM in orthodontics has seen the development of a new treatment for correcting malocclusions using “invisible” alignment trays, providing an alternative to conventional orthodontic treatment. Invisalign® is one of the many software solutions developed by CAD/CAM for orthodontics. This software is able to archive digital models obtained using optical impressions, schedule treatments by producing set-ups, and harness cephalometric data.
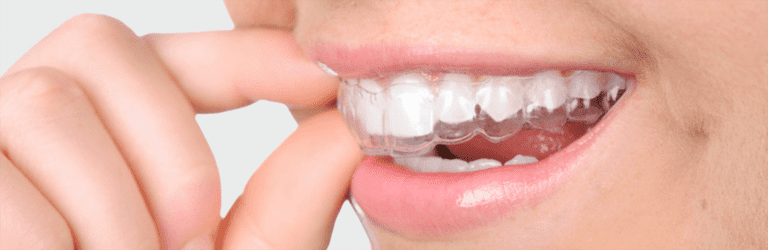
Figure 3 Invisible alignment tray
With CAD/CAM, the bonding stage is optimised by making an indirect bonding tray that can transfer the position of orthodontic brackets quickly and accurately onto the patient’s teeth. CAD/CAM can also be used to make osteotomy and repositioning guides (in the case of Lefort ortho-surgery and mandibular reconstruction), to make DFO braces, interception devices and models, etc.
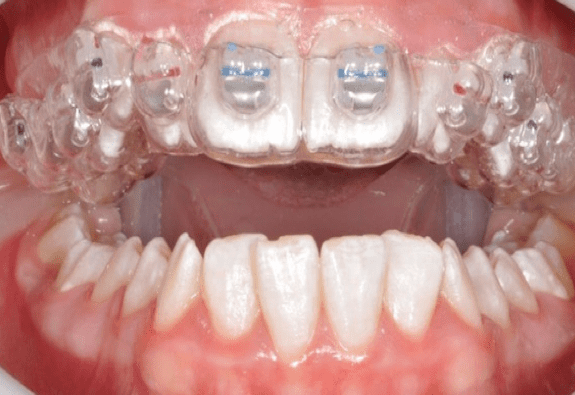
Figure 4 Gutter for indirect orthodontic bonding
What are the advantages of the CAD/CAM technique?
This technology offers myriad advantages, not just for dentists but also for patients and prosthetists.
For practitioners:
Quick, time-saving and easy to use:
The use of optical impressions eliminates a certain number of stages in the prosthetic chain. This translates into speedy and efficient operations, therefore saving considerable time and generating a standardised protocol with less need to fine-tune restorations, while still ensuring reliability.
Productivity and profitability increases:
Aside from productivity in the surgery, which is optimised by shorter manufacturing timeframes, the number of sessions is reduced to just one single session using direct CAD/CAM. This will guarantee day-to-day profitability for the surgery.
Greater accuracy, uniformity and traceability:
The rational protocol posited by CAD/CAM, which reduces the number of stages in the prosthetic chain and therefore the risk of error, makes restorations more accurate.
Furthermore, digital can be used to ensure consistency of medical devices and optimise their traceability.
Expanded therapeutic arsenal:
The practitioner has new materials and processes at their disposal, including 3D printing, which allows them to diversify any actions undertaken and treatments issued on a daily basis. Mastering the digital technique involves a training phase learning to handle new materials, and understanding their specific properties, indications and limitations, as well as new work tools, from intra-oral cameras and impression scanners (silicon or alginate) to numerical control machine tools (NCMT), and CAD/CAM software. This enables practitioners to develop their professional skills on a daily basis.
Improved brand image:
The wide range of materials and new therapeutic solutions afforded by CAD/CAM mean that practitioners can set themselves apart from the competition by enhancing their work and their surgery’s technical platform, and offer their patients a more modern form of dentistry.
For patients
Better quality treatments given:
The CAD/CAM technique means that patients can now enjoy restorations that are not just more aesthetically pleasing, biomimetic and biocompatible but also more accurate.
Dematerialising tasks throughout the prosthetic chain avoids accumulating the inaccuracies inherent in traditional techniques. With the advent of new, innovative materials, we now need to quickly develop safety and quality standards pertaining to the finished product which would ensure that restorations carried out using CAD/CAM would be of outstanding quality.
Patient comfort:
Eliminating the physical impression stage (alginate or silicone), often deemed too aggressive by CAD/CAM patients, has very significant benefits. Using just one anaesthetic instead of two, and eliminating an interim stage are two undeniable advantages. Sessions are shorter and more comfortable, and there are fewer of them; some treatments can even be carried out in one single session that includes preparation, thanks to direct CAD/CAM.
Reduced cost
Shortened timeframes and reduced human resources required to produce CAD/CAM restorations, coupled with a burgeoning market, have seen a fall in the cost of the treatment.
Advantages for the prosthetist
Advantages for the surgery become advantages for the laboratory. The prosthetist instantly receives a highly accurate digital impression, which reduces the source of errors that can sometimes occur through subjective interpretations, thereby making the whole process speedier and more productive.
Optimising communication in the Patient-Practitioner-Prosthetisttrio:
Practitioner-Prosthetist
With semi-direct and direct CAD/CAM, the practitioner communicates with the specialist laboratory in real time online, which results in a meaningful dialogue between both parties in their relative fields of expertise.
Patient-Practitioner
The digital data flow makes communication with the patient much easier. These technologies can be used to multiply information and exchange interfaces. In essence, the justification for a particular therapeutic choice and treatment plan is given by a straightforward and accurate visual explanation, with images displayed on the screen. Patients are then able to discuss with the practitioner the shade and form of the teeth, and the technique to be used. By dispensing with medical jargon, patients are better able to virtually visualise the end result of their treatment, and are reassured about the quality of this treatment. The surgery sees a rise in its credibility and a relationship of trust is established between both parties.
Ecological benefits
Reducing the volume of materials used in conventional techniques and minimising waste, particularly through the use of optical impressions and additive manufacturing, has an undeniably positive impact on the environment.
Limitations of the CAD/CAM technique
Despite the numerous advantages mentioned previously, a considerable number of practitioners remain reluctant to adopt CAD/CAM in their day-to-day practice. There are several reasons for this:
- High investment and maintenance costs, especially for young practitioners or small surgeries.Nevertheless, market developments will eventually lead to a fall in these costs.
- Prosthetist partner not qualified
- Lack of interest in and time required to adopt the CAD/CAM technique
- Aesthetic appearance of machined ceramic often deemed inferior to the stratified ceramic used in traditional techniques.
- Limited clinical indications
Conclusion
The advent of CAD/CAM has revolutionised the world of dentistry. This technology has paved the way for new therapeutic possibilities, as well as the development of new materials.
Despite the sharp growth observed in CAD/CAM, the number of dentists using it in France remains low. For some, converting is a major transition that will destabilise their practices.
The undeniable improvements in accuracy, time and comfort for both practitioner and patient are reasons to encourage more dentists to take the plunge and embrace digital dentistry.
When acquiring a dental CAD/CAM chain, it is important to choose appropriate equipment in terms of performance, ergonomics and, above all, compatibility.